Surface Treatment Alternatives for Sensitive Substrates
Surface Treatment Techniques: Corona vs Plasma vs Excimer
Table of Contents
This article is designed to let you know exactly what your surface activation options are, and allows you to make the right choice for your business. We will study the difference between the three main technologies in the field:


Ushio Europe has prepared an additional educational resource which shares the technology and defines the science behind its excimer technology. You can view the resource immediately by clicking here, or by selecting the Excimer: The Technology Explained link at the foot of this page.
Excimer is the alternative solution in industries dominated by corona and plasma
As an attractive alternative to tried and tested corona- and plasma-based solutions, excimer comes across as a newcomer to the market. You may not realise it, but this is a total fallacy, since excimer is not a new technology at all. Despite this, VUV surface irradiation has remained largely overlooked, even when surpassing other techniques in certain applications.
Yet Ushio Europe has persevered by continuing to discover and perfect excimer applications for over a quarter of a century. Since the application potential of excimer shows no sign of slowing, a growing crowd led by the aviation and automotive industries are beginning to wise up and take this old boy seriously.
Even representatives of other exhibitors at the show are peering over to see what all the fuss is about. The very same people wax lyrical on corona and plasma as the best available options, exposing a confused tone when admitting that they don’t know what excimer is; or their business has simply disregarded it as a benign threat.
Why? For want of a better phrase – blissful ignorance. Don’t get us wrong, these other surface treatments are good at what they do, and provide many businesses with a decent solution. Yet in order to understand which solution is best for your industrial process, you must first understand what your options are.
Corona Surface Treatment
The corona effect is actually based on the creation of plasma, which enters a state of ignition in normal air when influenced by a high-voltage electrode and a grounded back-roll placed behind the substrate. Within the plasma, atoms and molecules, such as oxygen, become excited and are accelerated at the surface of the substrate.
As this matter hits the surface, it violently sputters the substrate. Sputtering is a significant energy transfer that leads to chemical reactions, but also results in the integration of excited molecules into the molecular structure of the substrate. These accelerated molecules carry a lot of weight and their impact on the substrate surface results in a significant heat load.
Taking place under normal atmospheric pressure, corona is certainly the most affordable plasma treatment on the market, but as the oldest, it has been surpassed by the effectiveness of atmospheric plasma, vacuum plasma, and excimer solutions. Crucially, the lower plasma density ionises less surface molecules that the others, and with that, there is a distinct lack of surface chemistry selectivity.
Corona treatment is best suited to in-line procedures such as plastic film treatment, due to its two-dimensional limitations. Still, the top draw for corona users remains the robust usability and reduced price.
A significant downside of the corona discharge treatment, however, is the occurrence of some undesirable by-products. As a major source of static charge, corona treatment suffers from potential side effects that can cost an industry millions. Aside from forcing production to take place at a slower, static-free speed, the generation of static electricity can cause electronic interference, shocks to personnel, and even fires & explosions. From a product quality perspective, the ‘silent killer’ for corona-based industrial processes is the attraction of dust to highly charged surfaces.
As many substrates, such as plastics, gain a large static burden on their surfaces, they can attract dust from more than a metre away. While this can be remedied at a cost, by installing two static diffusers at strategic points, this is simply not an issue when using Ushio excimer solutions.

Corona's generation of static electricity can cause electronic interference, shocks to personnel, and even fires & explosions. With Ushio's excimer solutions, this is simply not an issue.
Plasma Surface Treatment
Most plasma technologies allow the surface treatment of three-dimensional objects, unlike corona, and are preferred for producing surface activation results on substrates that require a longer exposure before proceeding to the next stage of assembly. Plasma treatments cost more to operate in-house, however the coveted improvement in effectiveness is easily maintained through the control of gas type, pressure, concentration, and flow.
Within the nozzle, a very high power density accumulates. The result is an increase in total plasma density and so enhanced ionisation of molecules on the target surface can be observed, however, on the surface this is concentrated on a small area of the substrate. This is where plasma really comes into its own.
There are several types of plasma surface treatment, including atmospheric plasma, vacuum plasma, and Ushio’s excimer lamp surface treatment technology.
Atmospheric Plasma Surface Treatment
The ignition of atmospheric plasma takes place in the presence of a round electrode, either in normal air or in a noble gas such as argon. The ignited particles are then blown onto the substrate to begin surface activation. Like corona, this effect is based on the use of heavy, accelerated particles, leading to a more stressful impact on the surface of the substrate. There is a decreased electrical field and a much lower heat load, compared to corona treatment, but these factors are still side effects that do not impact excimer treated surfaces at all.
Vacuum Plasma Surface Treatment
Vacuum plasma is much the same as atmospheric plasma yet, due to the conditions in the requisite vacuum chamber, far less voltage is required to ignite the plasma. There is increased precision in the control over the small amount of noble gas or N2 used in the process. There is zero interaction from other gases and very little heat, thanks to low molecule speeds. The downside to vacuum plasma treatment is its confinement to a chamber, negating any potential roll-through processes.
Excimer Surface Treatment
The Ushio excimer effect is created by using a specially coated, noble gas filled VUV 172 nm lamp that emits high-energy photons. These light particles travel through the air, partly absorbed by oxygen and thus creating ozone on the substrate, where they crack the molecular bonds of the surface. The cracked molecules are partly removed, creating a chemically treated top layer of the substrate. This effect is distributed along the length of the lamp, which can, of course, be customised to your needs.
As an alternative to corona- and plasma-based treatments, excimer’s cold light drastically reduces the excess heat produced by comparable IR methods. In fact, there are only negligible IR emissions with excimer. The benefits of excimer do not stop there.
Excimer: The Gentle, Static-Free Alternative to Corona and Plasma Surface Treatment
Corona and plasma are both electrical discharge methods, so the object being treated receives a rather violent molecular impact to its surface. Electrical discharge occurs when fluid in the air surrounding a conductor is ionised, which in the case of corona and plasma, is created by applying a high-voltage between two electrodes.
Excimer utilises VUV light to treat the surface, so there is no discharge reaction or damage to your substrates. The photons emitted from the excimer lamp maintain a relatively low energy compared to the accelerated particles in other treatment methods. This softer approach means the substrate surface does not become rough, a far cry from the damage caused by corona and plasma.
Viewing a discharge-treated surface under an electron microscope will reveal a moon-like surface with large scattered holes, as a result of molecular bombardment. When viewing the same material type after excimer treatment, the surface remains smooth, benefiting from a higher level of homogeneity, thereby promoting enhanced adhesive qualities. Ultimately, the lower heat load from the ‘cold’ light of excimer and negligible IR emissions makes it an ideal solution for temperature sensitive materials, such as foils.
Thanks to the absence of an electrical field, excimer does not suffer from dust contamination like the aforementioned alternatives, and can be applied to all electronics, which would otherwise suffer from static related issues associated with a discharge.
Introducing the Ushio ExciJet series
- Facilitation of line spectra and broad distribution
- Instant on / off functionality without heating or cooling cycles
- Compact size of ExciJet modules enables enhanced manoeuvrability
- Easy control system and built-in power supply
- Scalability allows for potentially unlimited lamps & modules


- Compact, customisable plug-and-play modules for laboratory testing
- Robust, dimmable, mobile solutions for industrial applications
- High homogeneity and optimisation for the manufacture of semiconductors
- VUV output of over 170 mW/cm2 cleans up to 300 m/min in LED panel production
- Development & production satisfaction supplemented by an expert after-care team
Excimer technology ensures safety through clearly defined UV wavelengths
Emitting ultraviolet rays at an ideal 172 nm, Ushio’s research into vacuum-ultraviolet (VUV) excimer technology is leading the way to safe treatment of sensitive composite films, curing of new nanocomposite coatings, and plays a significant role in the production of carbon nanotube reinforced composites.
Excimer began generating significant interest from aerospace and automotive firms who wish to explore the weight reduction possibilities of photobonding and the elimination of adhesives. Dielectric barrier discharge excimer lamps hold a unique ability to bond materials, such as polymers and glass, without epoxy or other chemicals. By pressing two non-identical substrates together during treatment, a permanent bond is formed at a low pressure & temperature.
VUV light also enjoys a rather shallow penetration depth which leaves a thin polymerised film on the upper layer of UV-curable coatings. This effect leaves deeper layers unaffected, yet the resulting shrinkage leaves behind a homogeneously matted finish and brings scratch resistance to your composite coatings.
In general, ultraviolet light has the deserved reputation of being dangerous for humans; most notably at the wavelengths of 254 nm and above which are commonly used in conventional UV treatments. At 254 nm, UV light has enough intensity to penetrate the epidermal layer of skin and cause molecular changes in the layers beneath.
The excimer irradiation solutions from Ushio occupy customisable excimer wavelengths between 170 nm and 350 nm, which are chosen for the specific qualities achieved at each individual wavelength. Our surface activation technology has been developed to concentrate 172 nm light on your chosen substrates.
At certain wavelengths in this range, from 200 nm to 230 nm, the UV radiation is unable to penetrate the top layer of skin and simply deactivates any bacteria that may be present on the surface.
- Unlimited lamp capacity
- Phosphor-generated wavelengths from 170 nm – 350 nm
- Range includes 55 mm 9 W lamps up to 2 kW with our 2600 mm lamps

Compare Results at Ushio’s Excimer Application Laboratory
Ushio has seen a huge increase in enquiries about its excimer solutions, culminating in regular and popular appearances at trade shows such as JEC World, Composites Europe, InPrint, K 2019, and LOPEC.
The live demonstration is typical of the applications tested at the Ushio Excimer Application Laboratory, and serves as an illustration of the simple set of processes Ushio follow to ensure optimal standards for your bespoke implementation.
Reinforcing their commitment to finding a unique solution to its customers needs, Ushio Europe has completed the construction of their Excimer Application Laboratory. The Japanese multinational, which entered the European market in 1985, can now bring the development of vacuum-ultraviolet (VUV) applications to the fore.
Attracting visitors to the Ushio Germany facility in Steinhöring, Germany, prospective clients are welcomed with an exclusive opportunity to explore, develop, implement, and improve industrial processes. With more than 95% of the worldwide excimer lamp market, Ushio are sending a clear signal of their intention to lead from the front, by providing a full research & development service to their clients. This expansion of the European testing facility, shared with eminent horticultural subsidiary BLV, follows the success of similar IR and UV ventures by Ushio, Inc. in Japan and Ushio America.
The simple clean room concept is designed to put prospective excimer solutions through their paces, with each set of tests run with the intention of optimising one specific application. The only responsibility left for the client is to send, or show up at the lab with, relevant material samples for the tests. The in-house experts at Steinhöring design unique solutions in direct cooperation with the client, handing control to them to get the result they need, but maintaining a level of mentorship when needed.
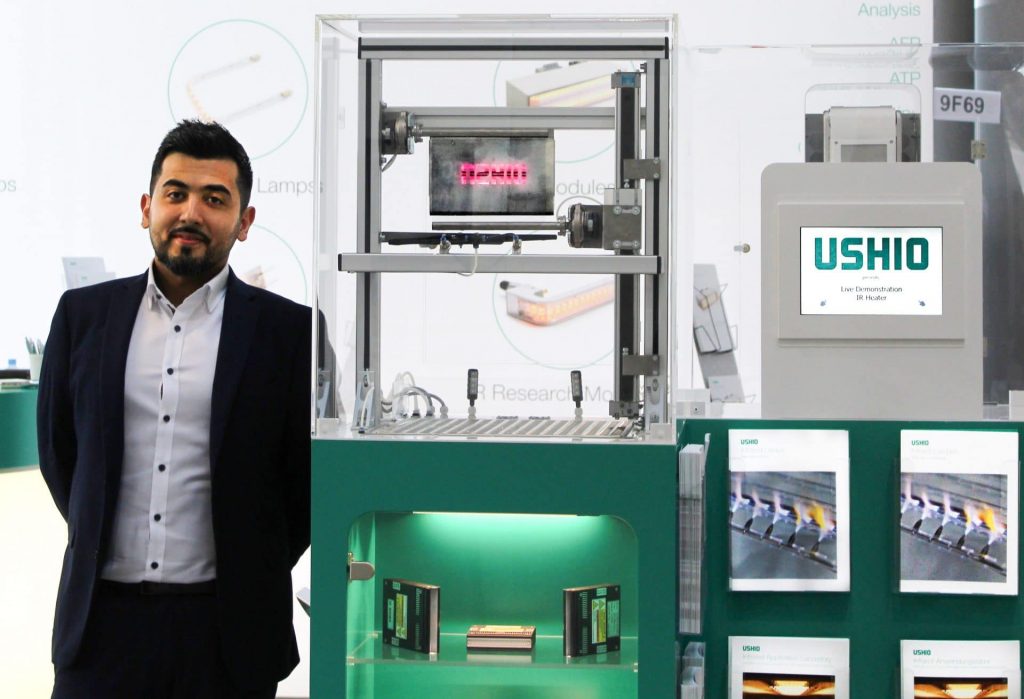
The excimer technology developed by Ushio has already earned an excellent track record in the following industrial processes:
- Surface activation
- Surface cleaning
- Surface modification
- UV curing
- Matting
- Curing nanocomposite coatings
- Disinfection
- Pre-treatment for coating of composite materials
- Optical, adhesive-free bonding (Photobonding)
- Removal of contaminants from production processes
- Photochemical or biological modification of gases, liquids, etc.
- Sensitive composite film treatment
Dr. Söllner feels that the Excimer Application Laboratory gives his clients new freedoms when it comes to finding the right solution: “We knew that people were crying out for a facility designed to accommodate intensive research, conceptualisation, and design. Whether your interest lies in bonding materials to each other, you want to disinfect water, or you simply need to print onto a surface, we can lend you our knowledge and experience during the investigatory stages.
As soon as you set foot on-site, we are discussing the industrial or laboratory processes you wish to explore. From there, we develop a bespoke modular or all-in-one excimer solution. The best part of a visit to Ushio Germany is that they let you take an active part in the testing. After all, it is your application, not ours, so we give you a chance to witness the process, analyse the data, and become completely comfortable with the results before making your final decision.”
Regardless of industry, the belated rise of excimer technology is already becoming a hot topic. Many companies are beginning to follow the lead of the aviation & automobile industries, by integrating their bespoke excimer solutions into existing production lines. If the adoption of excimer technology continues at this current rate, it could be the end of a dominant era for corona and plasma treatments. At the very least, excimer puts another worthy player on the field, challenging industrial competition and driving technological innovation forward, to bring better solutions across the board.
Fields and Industries Implementing VUV Excimer Surface Activation
- Aerospace
- Automotives
- Ecology
- Engineering
- Food and Beverages
- Forensic Science
- Medical Science
- Microelectronics
- Petrochemistry
- Photochemistry
- Photobiology
- Physics
Ushio Excimer Client Testimonials
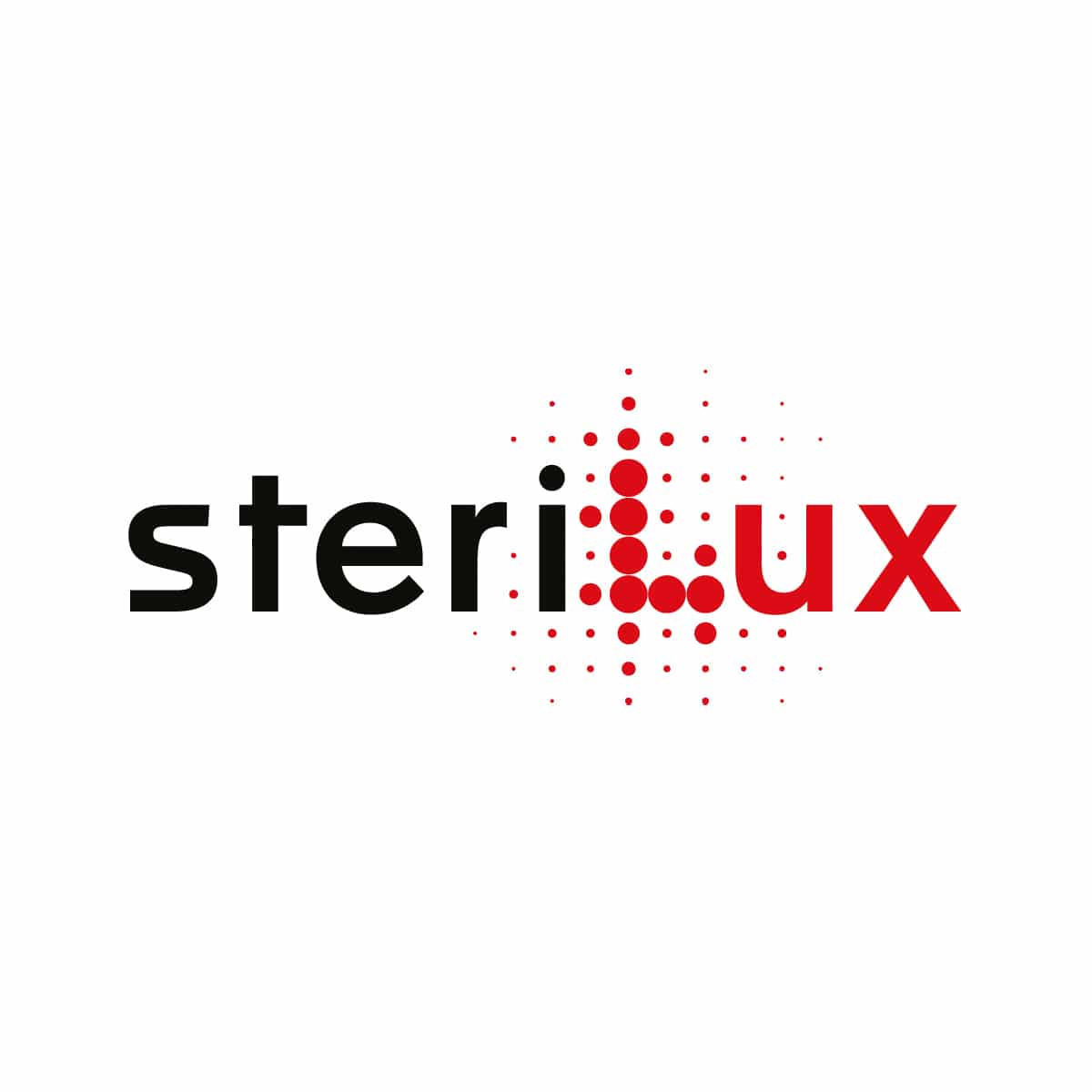
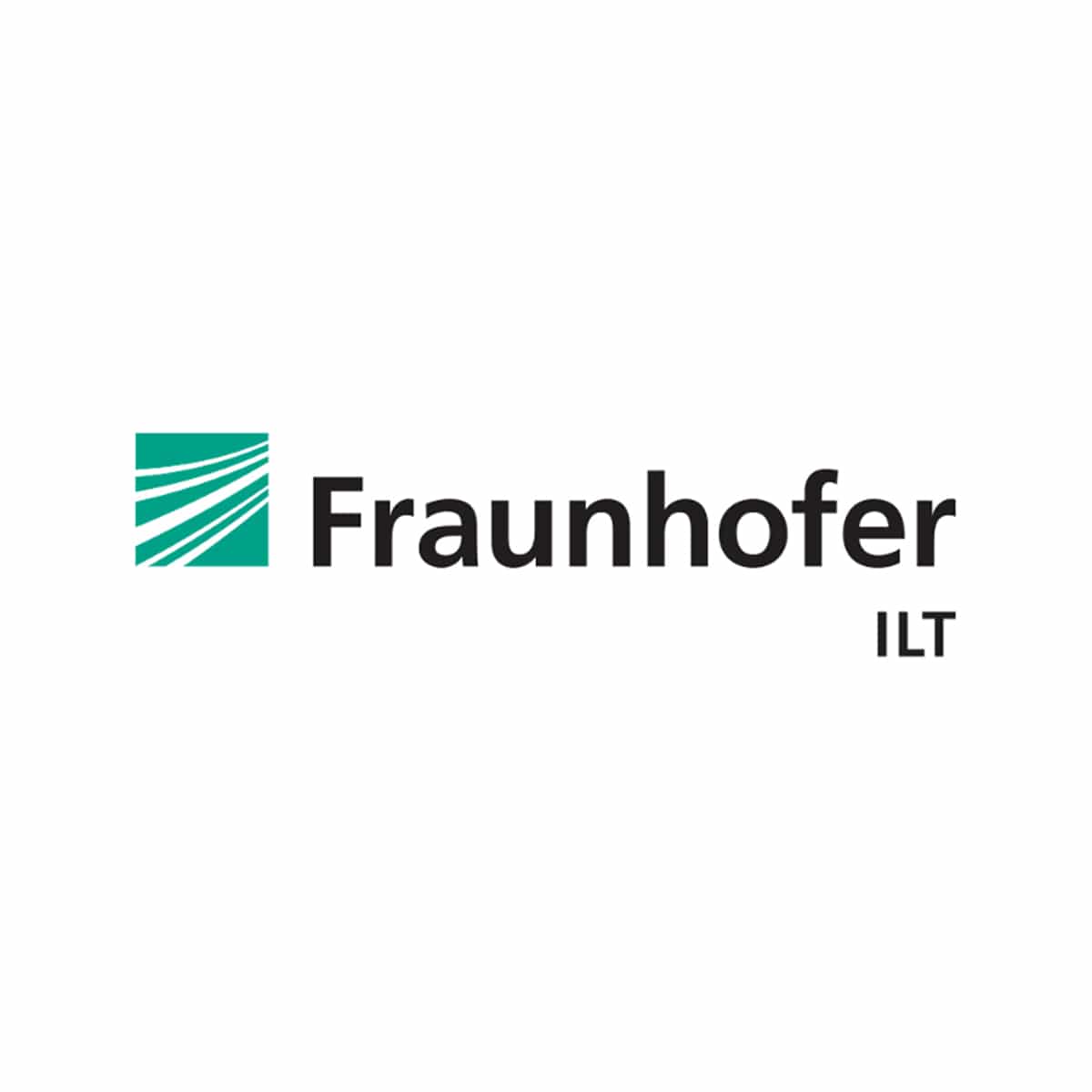
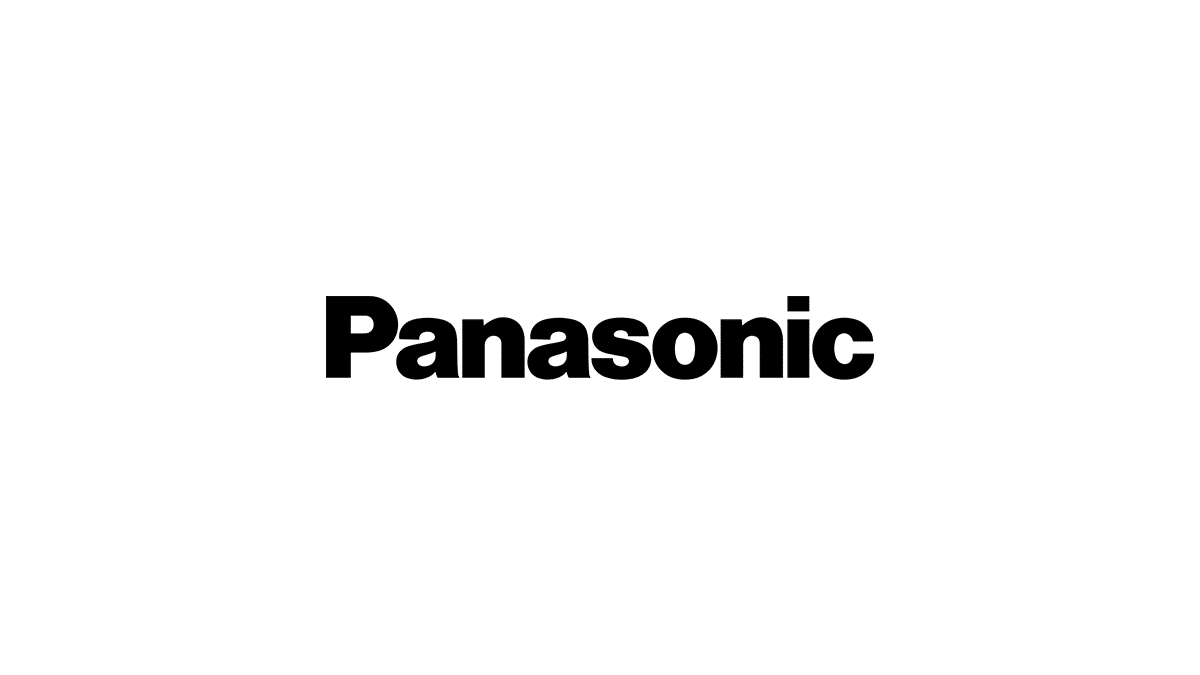
Contact Ushio today!